پوسته اکسیدی در دمای بالا، در فرآیندهای ریخته گری و اصلاح تختال تا نورد ورق از سطح محصول در دمای بالا جدا میشود.
در فرآیند نورد گرم شمش های فولادی، حدود 2% از فولاد نورد شده به صورت پوسته های اکسیدی ضایعاتی از خط تولید خارج میشود.
پوسته اکسیدی چیست؟
از نورد و قطعات فولادی، پوسته اکسید تولید میشود همچنین در تولید محصولاتی که به این عنصر نیاز دارند به عنوان یک ترکیب آهن دار مورد استفاده قرار میگیرد.
احیا پوسته اکسیدی
برای بازیافت یا احیای پوسته ها روش ها متعددی وجود دارد که یکی از این روش ها، احیای آنها به عوامل احیا کننده میباشد.
این عوامل احیا کننده در بستر ثابت و در دمای معین تحت عملیات احیا قرار میگیرد. عوامل احیا کننده شامل:
بازیافت این پوسته ها علاوه بر افزایـش بهره وری، صرفه جویی اقتصادی، همچنین کاهش هزینه خرید ده ها هزار تن آهن قراضه و سنگ آهن و انطباق بر مقتضیات زیست محیطی میباشد.
برای تولید تمامی محصولات فولاد در روش نورد گرم، پوسته ی اکسید یافت میشود مگر اینکه مثل ورقهای گالوانیزه در کوره های محافظ دار عمل ذوب آهن را انجام دهند.
در نورد گرم در درجه حرارت بالای کوره ها، مابین فولاد و مگنتیت یک لایه از Wustite و FeO وجود دارد.
85% از ضخامت پوسته اکسید در دماهای بالا که از FeO تشکیل شده است که حدود 10 تا 15 درصد آن Fe3O4 و 0.5 تا 2 درصد آن Fe2O3 تشکیل داده است.
هنگام سرد شدن آهسته(در دمای کمتر از Fº 1040 )، از نورد گرم در چرخش نوار کوره ای بیشتر FeO در آن به Fe3O4 تبدیل میشود سپس بعد از سرد شدن کامل فلز اکید آهن بیشترین مقدار را دارا میباشد.
کاربرد این ماده در شرایط احیایی بگونه ای است که فرآیند عادی کوره های قوس الکتریکی را تحت تأثیر منفی قرار ندهد مورد پایش قرار می گیرد.
کاربرد پوسته اکسیدی
کاربرد این محصول از سال گذشته در ناحیه فولاد سازی و در کوره های قوس با هدف صرفه جویی و اقتصاد مقاومتی مورد پیگیری قرار گرفت.
این ماده بدلایل سایش و آسیب رسانی به آسیاب ها در فرآیندهای عبور از احیا مورد استقبال قرار نگرفته است.
این ماده در شرایطی مورد پایش قرار میگیرد که فرآیند عادی کوره های قوس الکتریکی را تحت تأثیر منفی قرار ندهد.
پوسته اکسید آهن برای تولید فروسیلیس
یکی دیگر از کاربردهای مهم پوسته اکسید، استفاده از آن در تولید فروسیلیس میباشد.
فروسیلیس جوانه زا میباشد همچنین در فرآیند ریخته گری از آن برای ریز دانه کردن ساختار فولاد استفاده میشود.
فروسیلیس در چندین کارخانه صنعتی داخلی تولید میشود.
شایان ذکر است که کارخانه های تولید فروسیلیس مهمترین و همچنین اصلی ترین مشتری پوسته اکسید آهن کارخانه های فولاد سازی میباشند که به صورت مستقیم از کارخانه های فولاد سازی تغذیه میشوند.
برخی از این کارخانه ها با عقد قرارداد طولانی مدت با کارخانه های فولاد سازی نزدیک محل خود، منبع تامین سال های آتی خود را نیز تضمین مینمایند.
حمل و نقل پوسته اکسید آهن
این حمل و نقل معمولا در فروش های داخلی یا صادرات به صورت فله انجام میشود.
برای انتقال این محموله ها از کشتی های فله بر 10 هزار، 30 هزار و 50 هزار تنی استفاده میشود.
همچنین در انتقالات داخلی به دلیل راحت بودن تخلیه محصول از ماشین های کمپرس دار، جک دار برای حمل و نقل استفاده میشود.
موارد مصرف پوسته اکسیدی
پوسته اکسیدی در پروسه ی ریخته گری از سطح محصول در دمای بالا به دست می آید.
همچنین پوسته اکسیدی در فرآیند نورد گرم شمش های فولادی به شکل پوسته های اکسیدی ضایعاتی از بخش تولید خارج می شود.
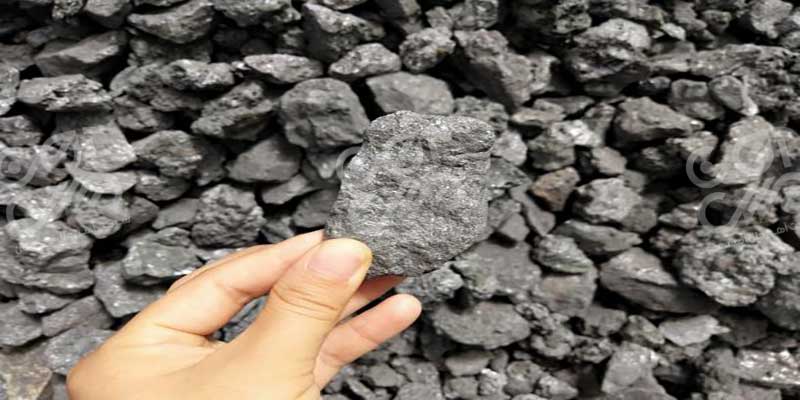
پوسته اکسیدی
از پوسته اکسیدی در ساخت کوره های بلند و تولید فروسیلیس استفاده میشود.
این پوسته ها مقاومت بالایی دارند چون نزدیک به 74 درصدشان آهن میباشد.
نتیجه گیری
بازیافت این محصول اهمیت بسیار زیادی از نظر اقتصادی دارد همچنین
همانگونه که ذکر کردیم برای بازیافت این محصول از روش های مختلفی استفاده میشود.
یکی از روشهای بازیافت این محصول استفاده از مواد احیا کننده میباشد.
مواد احیا کننده شامل زغال سنگ و گرافیت میباشد که با قراردادن آنها در یک دمای معین موجب بازیافت پوسته های اکسیدی میشود.
مواردی نظیر دما و اندازه زغال نسبت به پوسته در فرآیند احیای این پوسته ها بسیار تاثیرگذار میباشد همچنین از طریق این خصوصیات درجه احیا تعیین میشود.
این پوسته عموماً دارای رنگ خاکستری آبی یا استیل میباشد و یک پوشش بسیار نازک از هماتیت دارند.
جالب است بدانید که پوشش خارجی این پوسته ها با چشم غیر مسلح قابل مشاهده نیست.
همچنین از دانه های فلزی سیاه رنگی این پوسته ها ساخته میشود و باعث سخت تر شدن این فلز خواهد شد.
source: پوسته اکسیدی و فرآیند احیای آن