برای تولید آهن خام، سنگ آهن را در کوره های آهن گدازی تولید می کنند.
اساس تولید و ساخت آهن و فولاد، سنگ آهن می باشد.
برای تولید آهن معمولی، فولاد و چودن از آهن خام استفاده می شود.
چودن و آهن آلیاژهایی از آهن می باشند.
فلزات آهنی، پرکاربردترین محصولاتی هستند که 95 درصد از فلزات تهیه شده در سراسر جهان را تشکیل می دهند.
آهن فلزی وزنی سنگین دارد و به رنگ خاکستری و درخشان است، آهن فلزی از سنگ معدن آهن استخراج می شود.
چدن و فولاد قیمت پایینی دارند همچنین ترکیبات آهن این دو مقاومت بالایی دارد به همین علت استفاده در ساخت ساختمان ها، بدنه کشتی های بزرگ، اتومبیل ها مقرون به صرفه می باشد.
چودن و فولاد از آهن خام (سنگ آهن) تولید می شود.
همچنین آهن در صنعت ساختمان نیز کاربرد دارد که به صورت مقاطع فولادی دیگر مانند میلگرد، نبشی، ناودانی، میخ، پیچ و مهره، گالوانیزه رنگی و روغنی و… استفاده می شود.
سنگ آهن
سنگ آهن مخلوطی از نمک های معدنی، سنگ آهن، آلومین و … می باشد. که آن را در کوره های گداز حرارت می دهند ت محصول خام تولید شود تا بتوان از آن برای تولید آهن، فولاد، چدن استفاده کرد..
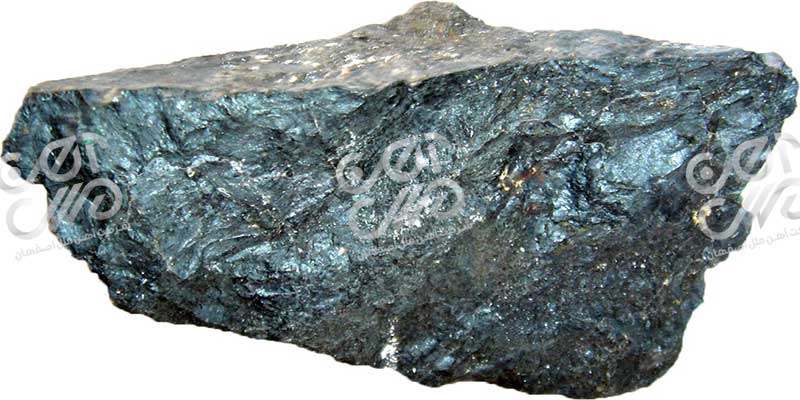
سنگ آهن
در کوره های آهن گدازی از 4 نوع سنگ استفاده می شود از جمله:
- هیدروکسیدها
- اکسیدها
- سولفور
- کربنات
انواع آهن خام
عامل تفاوت انواع آهن و فلزات آهنی، کربن می باشد. میزان کربن در آهن نیز، خاصیت و ویژگی آهن، فولاد و چدن را مشخص می سازد.
آهن خام به دلیل وجود حجم زیاد کربن در آن، ترد می باشد بنابراین قابلیت چکش خواری و نورد شدن را ندارد چون در اثر ضربه خرد می شود.
همچنین کربن دمای ذوب فلزات را کاهش می دهد.
آهن خام به دو دسته ی آهن خالص و آهن معمولی تبدیل می شود که میزان کربن در این دو نسبت به آهن خام کمتر است.
آهن معمولی
آهن معمولی حدود 2 درصد کربن دارد.
تولید آهن معمولی
آهن خام از طریق کربونیزاسیون آهن خام به همراه مقداری آهن قراضه در کوره ساخته می شود،
این آهن حدود ۲ درصد کربن دارد و از طریق کربونیزاسیون آهن خام به همراه مقداری آهن قراضه در کوره به دست خواهد آمد.
دمای ذوب آهن معمولی پایین است و حدود 1130 درجه سانتی گراد می باشد.
همچنین آهن در هوای نمناک زنگ می زند بنابراین نیاز به ضد زنگ و پوشش های محافظ دارد.
آهن معمولی کاربرد متعددی در ساختمان سازی، صنایع مختلف، ساخت ماشین آلات صنعتی دارد.
آهن خالص
آهن خالص همان آهن نرم و آهن ورزیده می باشد.
آهن خالص فقط 0.02 درصد کربن دارد و به دلیل مخلوط شدن مقداری سرباره با آن حالت فیبری دارد.
دمای ذوب آهن خالص حدود 1540 درجه سانتی گراد و این دما به نسبت بالا است، بنابراین علت جوشکاری با آن امکان پذیر نمی باشد.
این محصول انعطاف پذیر است و مقاومت کششی بالایی دارد، همچنین مقاومت آن در برابر خوردگی زیاد است.
آهن خالص مصرف ساختمانی ندارد و از آن برای تولید چدن و فولاد استفاده می شود.
آهن خام بر اساس ساختارهای کریستالی خود، به دسته های زیر تقسیم بندی می شود.
آهن خام سفید
در اثر سرد شدن آهن خام در سرعت زیاد آهن خام سفید تولید می شود.
دلیل رنگ سفید این محصول، کربن این محصول به سرعت سرد می شود، به همین علت رنگ آن روشن (سفید نقره ای) باقی می ماند.
در ساخت فلزات و فولاد سازی از آهن خام سفید استفاده می شود.
در آهن خام سفید مقدار سیلیسیم کم است و جنس آن سخت و ترد می باشد، همچنین سطح شکسته آن نیز دارای دانه های ریز و روشن می باشد .
آهن خام خاکستری
در اثر سرد شدن آهن خام در سرعت پایین، آهن خام خاکستری تولید می شود.
دلیل رنگ خاکستری این محصول، چون کربن آن در سرد شدن آهسته به گرافیت تبدیل می شود، رنگ آن تیره باقی می ماند.
از این محصول در ساخت چدن استفاده می شود.
مقدار سیلیسیم موجود در آهن خام خاکستری زیاد است، همچنین این محصول ترد نیست و از آهن خام سفید نرم تر است، سطح شکسته آن نیز دارای دانه های درشت و خاکستری می باشد.
آهن خام نیمه خاکستری
از این محصول در تولید فولاد و چدن سخت استفاده می شود، جنس این آهن خام مابین آهن خام سفید و آهن خام خاکستری می باشد.
چدن چیست ؟
از آهن خام خاکستری، چدن تولید می شود.
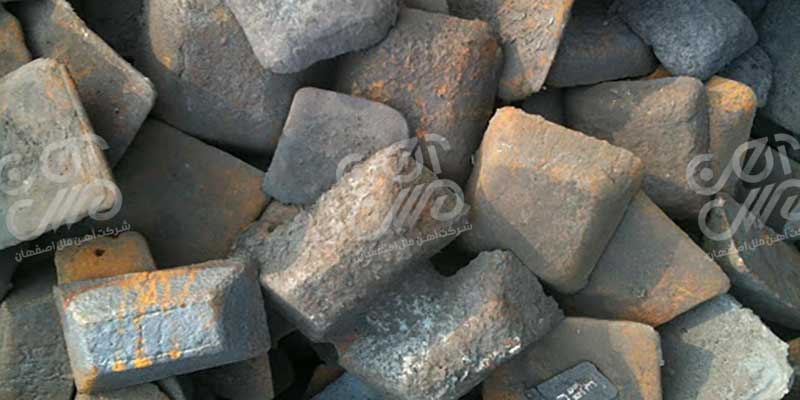
چدن چیست
این محصول با مقداری قراضه آهن در کوره های مخصوص ذوب می شوند تا مقداری از کربن آن بسوزد و ناخالصی هایی نظیر گوگرد و فسفر که خصوصیات آهن را تا حد زیادی تحت تاثیر قرار می دهند، به صورت سرباره خارج می شود.
حال این فلز مذاب که باقی مانده است حاوی مقداری منگنز می باشد، چدن نام دارد.
آلیاژهای چدن، آهن، کربن، منگنز و سیلیسیم است.
وجود آلیاژ منگنز باعث می شود که چدن را سخت کند، و وجود کربن در چدن باعث می شود که به صورت گرافیت درآید.
جنس چدن بستگی به سرعت سرد شدن آن و همچنین جنس آهن خامی دارد که برای تولید چدن استفاده می شود.
میزان کربن در چدن 3.5 – 2 درصد وزن آن است. نقطه ذوب این محصول بین k 1470 – 1420 است.
چدن بسیار محکم، سخت و شکننده میباشد.
همچنین چدن گرمای سفید موجب شکستن اجسام میشود قیمت نسبتا پایین و ویژگی های چدن سبب استفاده از آن در صنایع مختلف می شود، در صنعت ساختمان از چدن برای ساخت لوله های آب و فاضلاب، نرده، کف پوش، یراق آلات و … استفاده می شود.
خواص چدن
چدن همانند آهن خام، بدون حالت خمیری از جامد به مایع تبدیل می شود، بنابراین قابلیت چکش خواری خوبی دارا نمی باشد.
چدن سخت و شکننده است. مقاومت چدن در برابر آتش نسبت به فولاد بیشتر است و همچنین دیر زنگ می زند.
هریک متر چدن به ازای هریک درجه افزایش دما، 0.01 میلی متر افزایش طول خواهد داشت.
انواع چدن
چدن نیز مانند آهن، انواع مختلفی دارند و همه ی انواع آن ها در برابر فشار مقاومت بالایی دارند.
چدن سفید
در اثر سرد شدن چدن خام در سرعت زیاد، چدن سفید ساخته می شود.
رنگ این محصول به این دلیل سفید است که کربن آن در سردشدن سریع، به گرافیت تبدیل نمی شود و رنگ آن روشن ( سفید نقره ای ) باقی می ماند.
از این محصول در ساخت وسایل کوچک استفاده می کنند.
حجم سیلیسیم در این محصول کم است و جنس آن سخت و ترد است، به همین علت قابل سوهان کشیدن نیست.
سطح شکسته چدن سفید دارای دانه های ریز و روشن می باشد .
چدن خاکستری
در اثر سرد شدن چدن خام در سرعت پایین، چدن خاکستری تولید می شود.
رنگ خاکستری این محصول به این دلیل است که کربن آن در سردشدن آهسته، به گرافیت تبدیل می شود و رنگ آن تیره باقی می ماند.
کاربرد این محصول در پروفیل پنجره، یراق آلات، ناودانی، شبکه چدنی، لوله های چدنی، درپوش های چدنی کف خیابان ها و … مورد استفاده قرار می گیرد.
چدن خاکستری نسبت به چدن سفید نرم تر است، جنس آن سخت و شکننده بوده و قابلیت چکش خواری دارد.
سطح شکسته آن نیز دارای دانه های درشت و تیره می باشد .
چدن نیمه خاکستری
جنس آن بین چدن سفید و چدن خاکستری است.
چدن سخت
تولید چدن سخت به این صورت است که ابتدا چدن را گرم کرده سپس سطح خارجی آن را سریع سرد می کنند و صبر می کنند تا داخل آن به آرامی خنک شود.
به همین علت سطح آن چدن سفید و مغز آن چدن خاکستری همچنین این چدن دیر ساییده می شود.
از این چدن برای ساخت لوله های زیر دال پل ها استفاده می شود.
چدن نرم
برای بالا بردن مقاومت چدن در برابر ضربه همچنین بتوان آن را چکش کاری کرد،
تکه های چدن سفید و نیمه خاکستری را به همراه مقداری گرد سنگ اکسید آهن حرارت می دهند تا بخشی از کربن آن بسوزد.
با این کار تردی چدن کم شده و نرم می شود.
از چدن نرم در ساخت وسایل وسایل کوچک نظیر یراق در و پنجره، کلید و قفل، شیر آب و … استفاده می شود.
فولاد چیست؟
یکی از معروف ترین آلیاژهای موجود که مابین 0.2 – 1.5 درصد کربن دارد، فولاد می باشد. فولاد از پرمصرف ترین فلزات آهنی است.
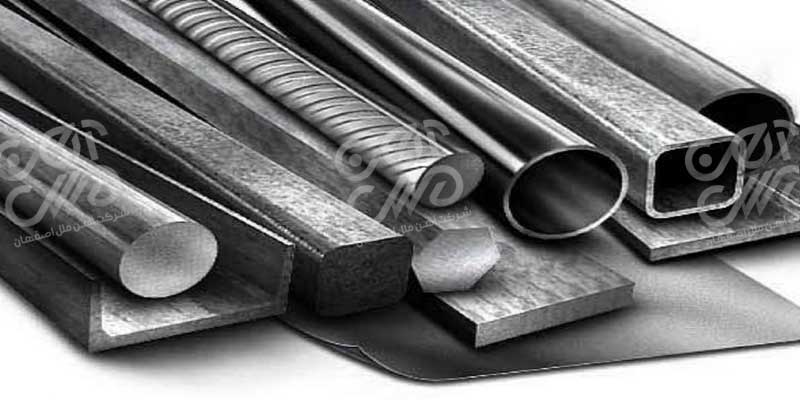
فولاد چیست
امروزه تقریبا ۵۰ درصد تولید کنونی فولاد در دنیا از آهن قراضه است به این صورت که آهن خام سفید را با مقداری قراضه آهن ذوب می کنند تا کربن خود را از دست بدهد و برخی از ناخالصی های آن نیز به صورت سرباره خارج شود و فولاد تولید شود.
خواص فولاد
یکی از مهم ترین مصالح ساختمانی که قابلیت شکل پذیری و مقاومت زیادی دارد فولاد است.
خواص فولاد به مواردی چون عملیات حرارتی انجام شده بر روی آن، فلزهای آلیاژدهنده موجود در آن، درصد کربن موجود در آن بستگی دارد.
خواص فولاد به عملیات حرارتی انجام شده بر روی آن بستگی دارد.
با افزایش دما تا ۱۰۰ درجه، فولاد ۲ درصد منبسط می شود.
فولاد قابلیت شکل پذیری دارد و می توان آن را به هر شکل دلخواهی در بیاوریم.
با استفاده از اتصال خشک (پیچ و مهره یا تا کردن) و اتصال تر (جوشکاری) می توان قطعات مختلف فولادی را به یکدیگر متصل کرد.
فولاد در برابر رطوبت و نمک ها به سرعت زنگ می زند و یا پوسیده می گردد.
برای مقابله با زنگ زدگی فولاد می توان عناصری نظیر کرم، مس، وانادیم و نیکل را به آلیاژ آن اضافه کرد.
همچنین برای جلوگیری از زنگ زدگی فولاد، می توان سطح آن را قلع اندود (حلبی)، روی اندود (آهن سفید) و یا با مواد آلی و پلاستیکی رنگ کرد.
مقاومت کششی در فولادهای مختلف متفاوت می باشد.
مقاومت فشاری، برشی، خمشی، ضربه ای و سختی فولادهای مختلف بر حسب آلیاژ آن ها متفاوت است.
خواص مکانیکی فولاد را می توان با عملیات مختلف گرمایی و سپس سرد کردن تحت شرایط مختلف تغییر داد.
سرد کردن فولاد می تواند به صورت سریع در آب یا روغن و یا به آهستگی به وسیله دستگاه خنک کننده یا در هوا صورت گیرد. تاثیر هریک از این روش ها بر فولاد متفاوت خواهد بود.
انواع فولاد
کلی ترین دسته بندی برای فولاد بر حسب میزان کربن در آن است که به شرح زیر می باشد:
فولاد نرم
در صد کربن در فولاد نرم حدود 0.2 درصد می باشد، از فولاد نرم در ابزارسازی نمی توان استفاده کرد.
کاربرد این فولاد استفاده در ساخت لوله، چرخ دنده، پیچ و مهره، سیم خاردار، ورق فولادی و تیرهای فولادی، استفاده در سازه ساختمان ها مورد استفاده قرار می گیرند.
فولاد متوسط
درصد کربن در این فولاد بین 0.2 تا 0.6 درصد می باشد، این فولاد در ساخت ریل، دیگ بخار و ماشین آلات به کار می رود.
فولاد سخت
از فولاد سخت برای ساختن کارد و چنگال، فنر، مته، ابزارآلات و … استفاده می شود.
درصد کربن در فولاد سخت مابین 0.6 – 1.5 درصد که زیاد می باشد.
با افزودن برخی عناصر به فولاد، تبدیل به فولاد ویژه ای می شود که جهت مصارف ساخت استفاده می شود.از جمله فولاد ضد زنگ، فولاد مقاوم در برابر گرما، فولاد ضدزنگ، فولاد مقاوم در برابر آب و هوا و غیره.
تفاوت آهن، فولاد و چدن
از پراهمیت ترین موضوعات در صنعت تولید و ساخت، توانایی شناختن چدن از آن می باشد.
آهن
از فولاد کم کربن، آهن تولید می شود. کیفیت این آلیاژ از درصد کربن مگنز پایین (کربن کمتر از ۰.۰۸ درصد و منگنز کمتر از ۰.۰۶ درصد) مشخص می شود.
فولاد
بیشترین حد کربن در فولاد، حدودا 2 درصد می باشد.
آهن مذاب تصفیه شده را با افزودن مقدار معین کربن و فلزهای آلیاژ دهنده مثل وانادیم، کروم، تیتانیم، منگنز و نیکل به فولاد تبدیل میکنند.
چدن
- چدن آلیاژی از آهن و کربن است که عموما ۳ تا ۵ درصد کربن و ۱ تا ۳ درصد سیلیسیم دارد.
- میزان کربن چدن، نسبت به فولاد بیشتر است. چدن ها گروه مهمی از آلیاژهای ریخته گری هستند.
- نقطه ی ذوب چدن نسبت به نقطه ذوب آهن پایین تر است.
- چدن نسبت به آهن در مقابل خوردگی آسیب پذیر تر می باشد.
- چدن بسیار خشک تر و خمش ناپذیرتر از فولاد و آهن می باشد.
source:تفاوت فولاد، آهن و چدن، از انواع تا کاربرد هریک در صنعت